Hydrogen Applications by MACEAS
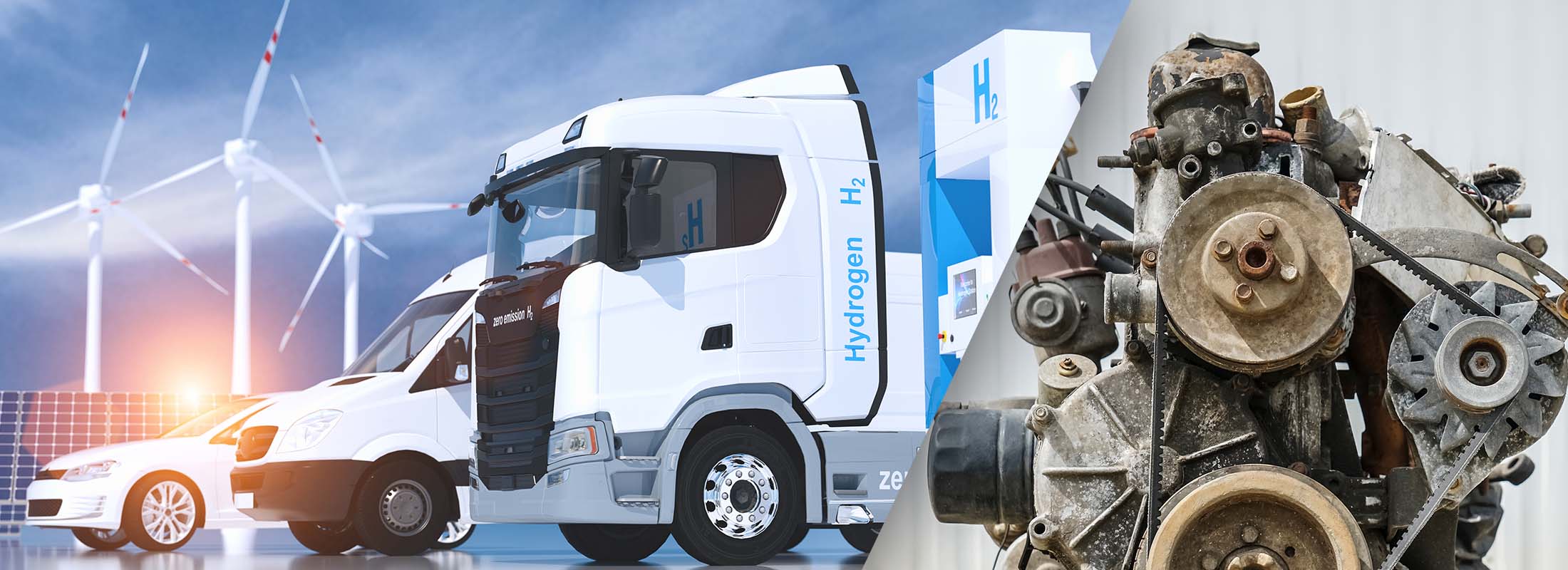
The combustion engine has had its day
By the end of this decade, electromobility will dominate the automotive sector more and more, while vehicles with conventional combustion engines will increasingly take a back seat. This is crucial to be able to achieve the set climate goals so that the man-made climate change can still be stopped or retarded.
In the passenger car sector, hybrid drives and battery solutions will be the drive technology of the future, but fuel cells and the use of hydrogen as an emission-free fuel will also play a major role in tomorrow’s mobility. The fuel cell drive is a real alternative, particularly in heavy-duty traffic, in commercial vehicles, in shipping, in the aviation sector, but also in local passenger transport and in special vehicles. Short charging times and a sufficient range per storage cycle are the main advantages of this concept. If the hydrogen is generated with renewable energy (e.g., wind power or solar energy), the climate balance is also positive – keyword “green hydrogen”.
Fuel cell vehicles combine numerous technical components under one roof. A correspondingly pressure-tight or cryogenic vessel or tank is required for hydrogen storage. The fuel cell, consisting of numerous individual components, generates the electricity required. In addition, there are buffer batteries, the electric motor, compressors, cooling units as well as pipe systems and many other components. And many of these components also have to be subjected to a leak test in order to meet quality standards and to ensure durability and reliability.
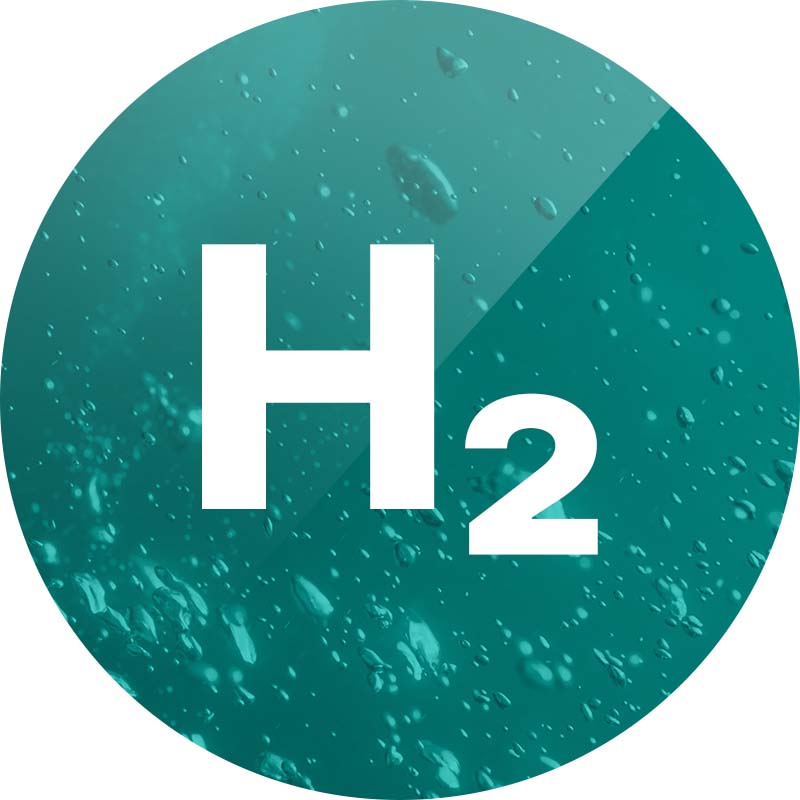
Hydrogen applications
Click on one of the areas to learn more about a specific application
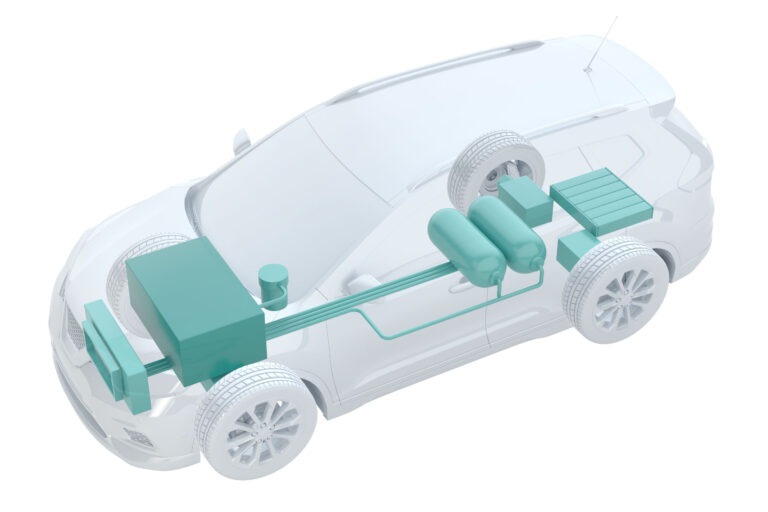
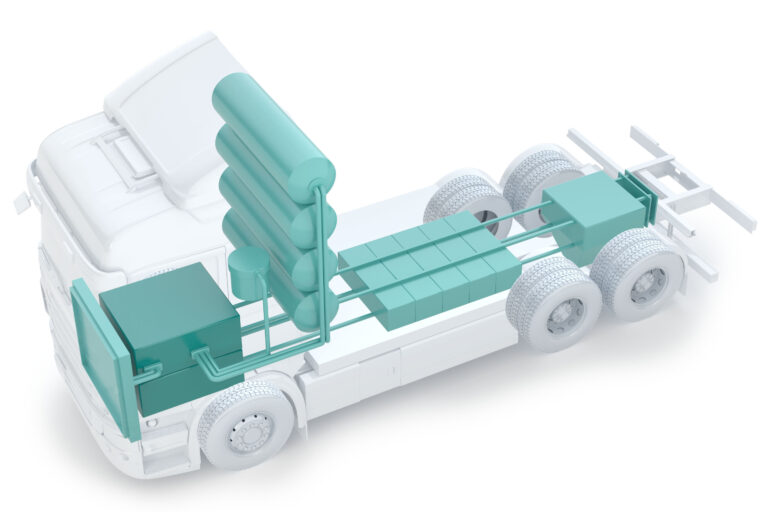
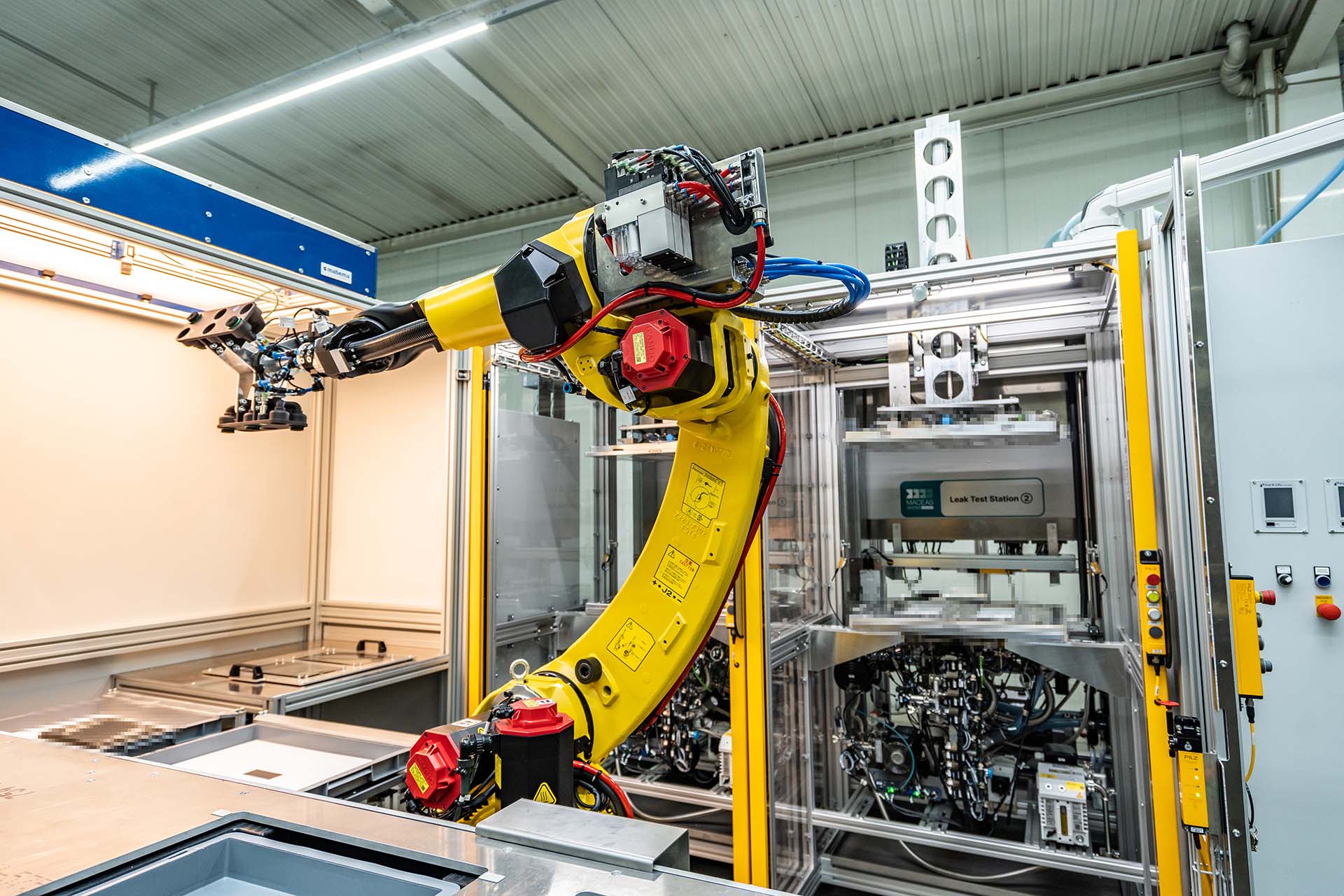
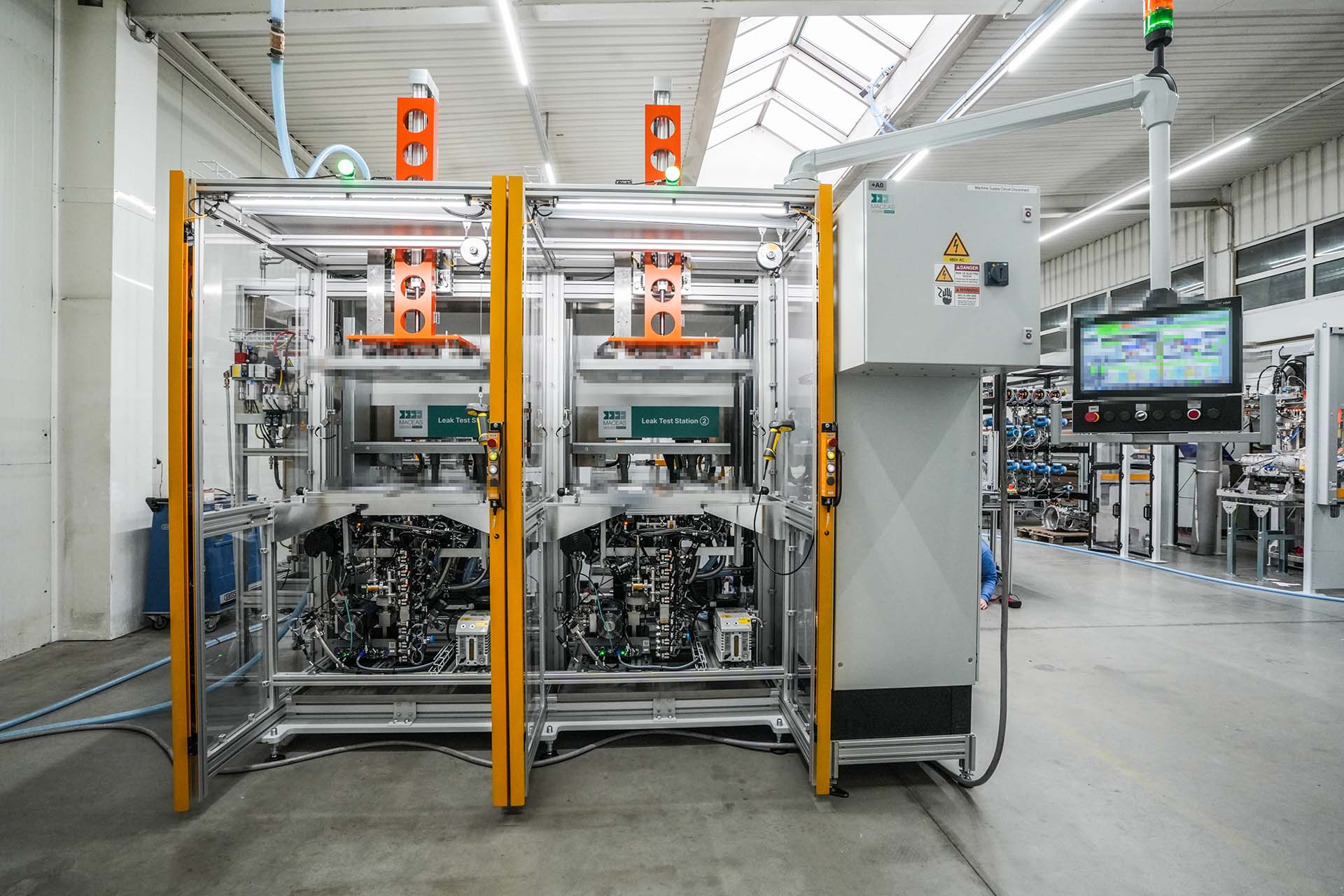
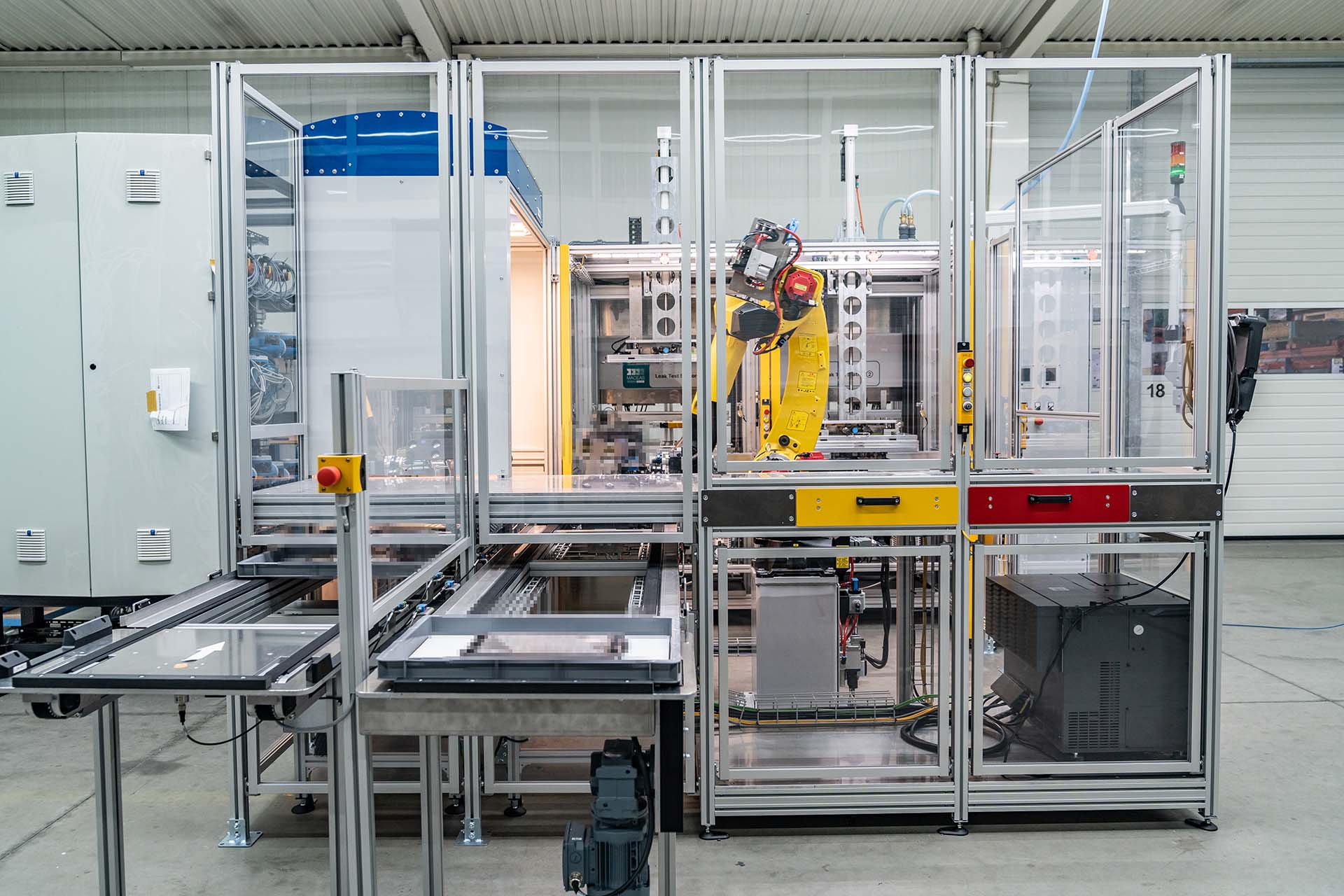
Fuel cells
The fuel cell is the heart of hydrogen-powered fuel cell vehicles. And here one component is particularly important, the bipolar plate of the fuel cell stack.
Our modular and scalable machine concept works with the helium vacuum method for leak testing of all three process circuits of the bipolar plates (cooling, hydrogen and oxygen circuit). The method enables the detection of particularly low leak rates and short cycle times. The scalability of the system allows it to be adapted to current market demands and production requirements.
Of course, we also offer a leak test of the assembled stack as well as the leak testing of other fuel cell components.
Learn more about our products and services in the field of leak testing for fuel cells on our information page:
Hydrogen vessel / tank
The current state of the art in the field of hydrogen-powered vehicles is based on gaseous hydrogen storage at 350 bar or 700 bar in a pressure vessel. Alternatively, there is also the possibility of storing hydrogen in liquid form at -253 ° C. The so-called cryogenic hydrogen vessels enable storage with a lower volume requirement and thus space requirement compared to gaseous storage.
We offer leak testing of both high pressure and cryogenic hydrogen tanks. The creation of a vacuum in the insulating intermediate layer of the cryogenic vessel poses a particular challenge. This is implemented in our system concept.
We offer both leak testing and vacuum generation in one overall concept.
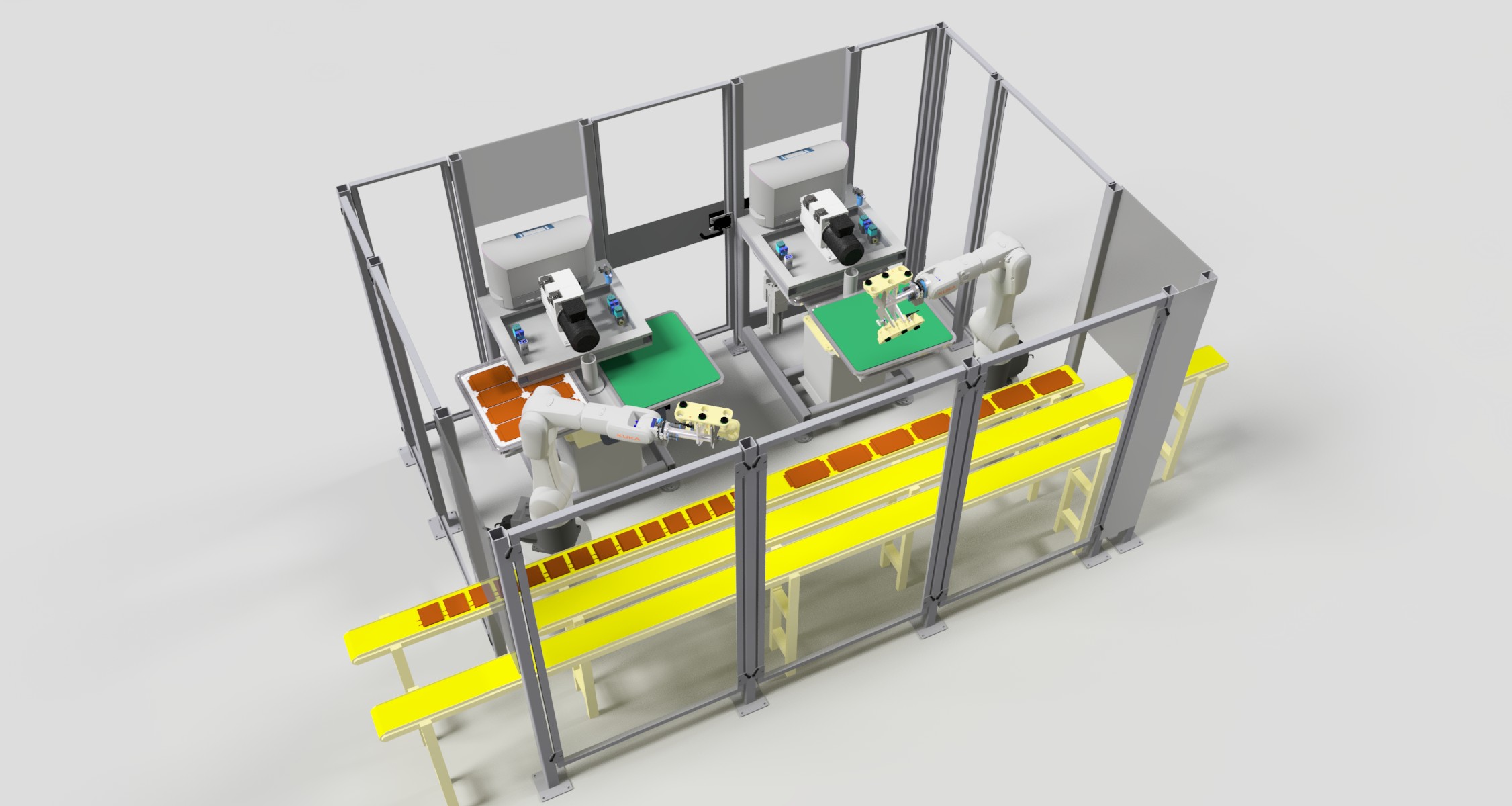
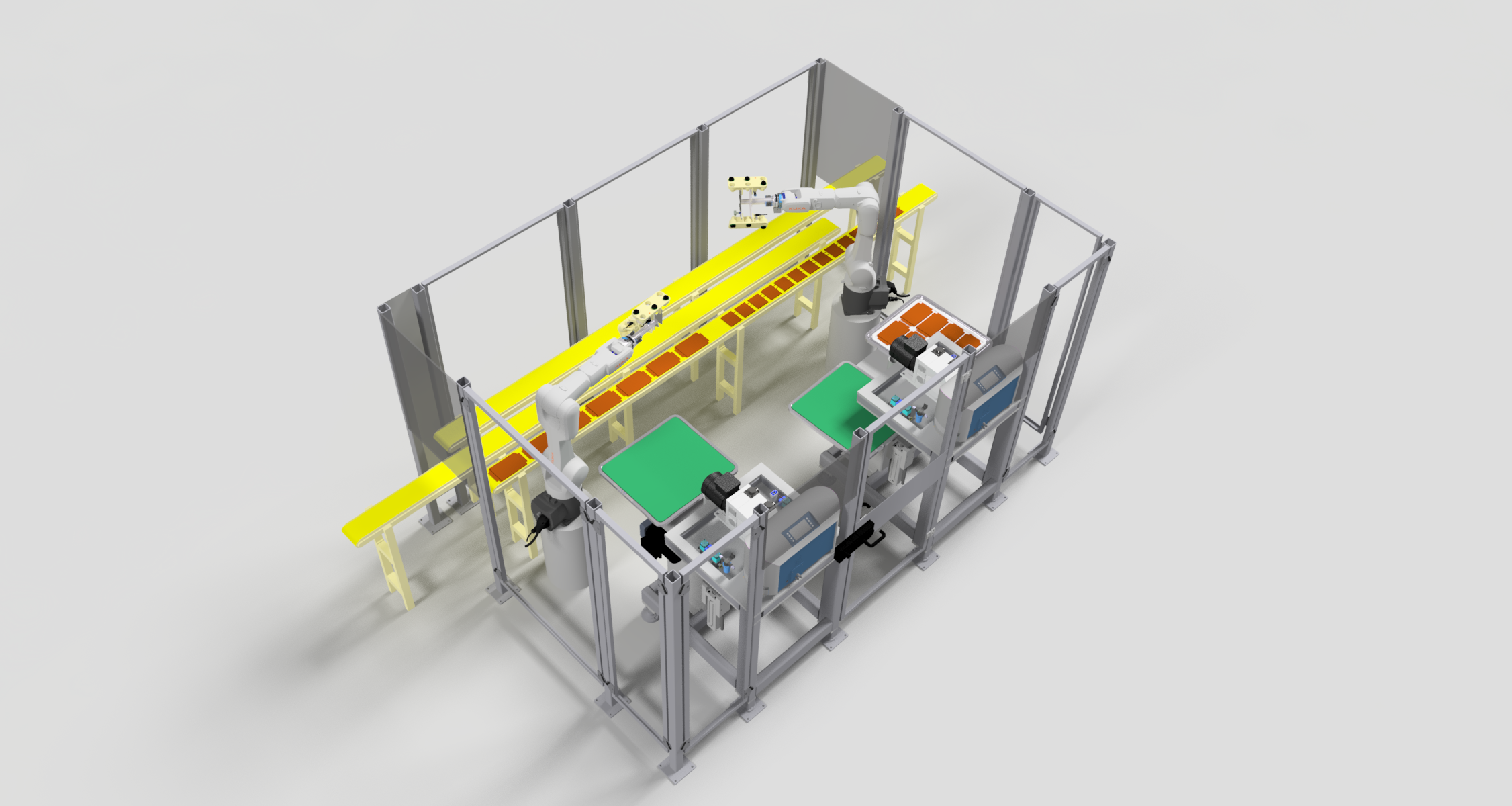
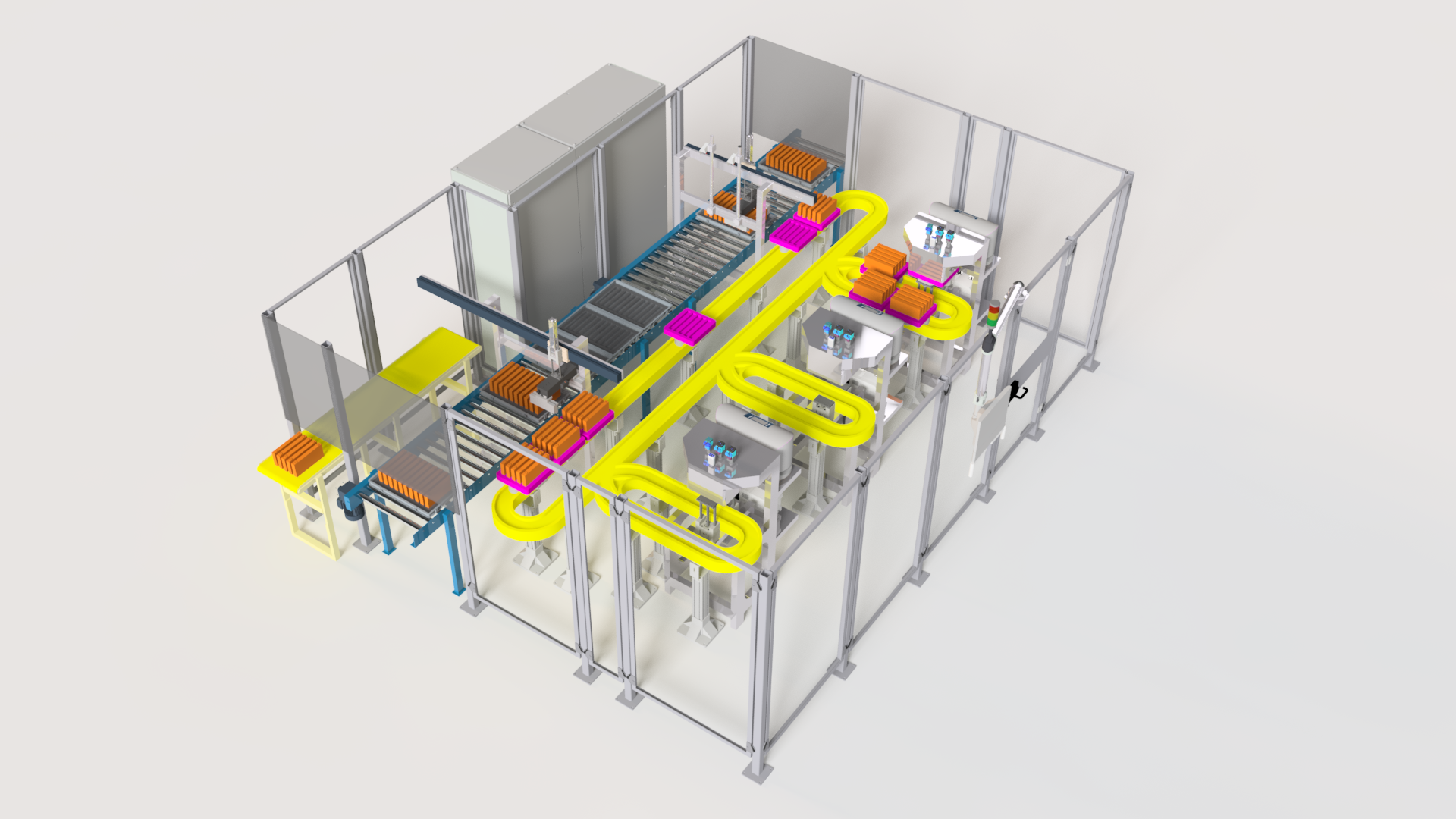
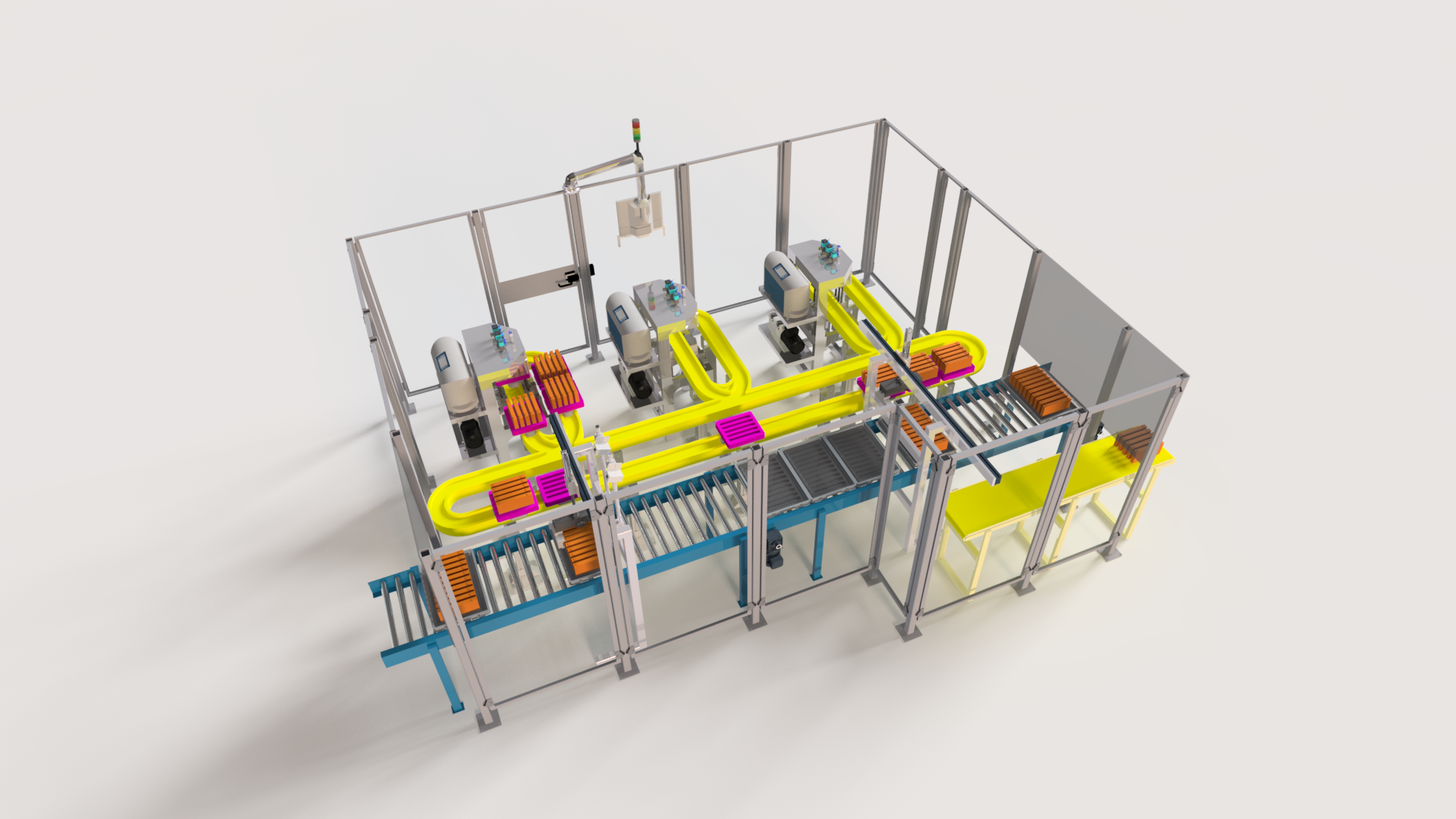
Battery
The lithium-ion battery is not only the main component of the Battery Electric Vehicle (BEV), but also part of a fuel cell vehicle. The so-called buffer battery compensates and buffers the fluctuations between power generation in the fuel cell and power use in the electric motor and is therefore an important component of the electrified drive train in hydrogen vehicles or Fuel Cell Electric Vehicles (FCEV).
Both the battery cell and the battery modules and packs demand high quality, safety and durability. The tightness as a decisive quality feature also plays a major role. Our leak testing systems enable the detection of very low leak rates, both in the case of the battery cell housings and covers or in an end-of-line test of the finished battery cell. There are also leak tests of the battery modules, cooling elements and the battery housings (packs).
Different leak test methods are available, such as the helium vacuum leak test of the battery cell housings and cooling elements, detection in a vacuum of electrolytes leaking from finished battery cells or (automatic) sniffing with helium of the battery modules and battery packs.
Learn more about our product and service solutions regarding batteries on our information page:
Cooling systems
Both battery-electric and hydrogen-powered drives require aggregates and systems to cool the batteries and fuel cells. The components of the cooling system, such as cooling housings, cooling pipes, cooling elements etc. are filled with very toxic coolants. Such coolants are not allowed to get into the environment and therefore a corresponding tightness of the components is essential. For this reason, a high-quality and reliable leak test is required as part of the quality assurance of the components.
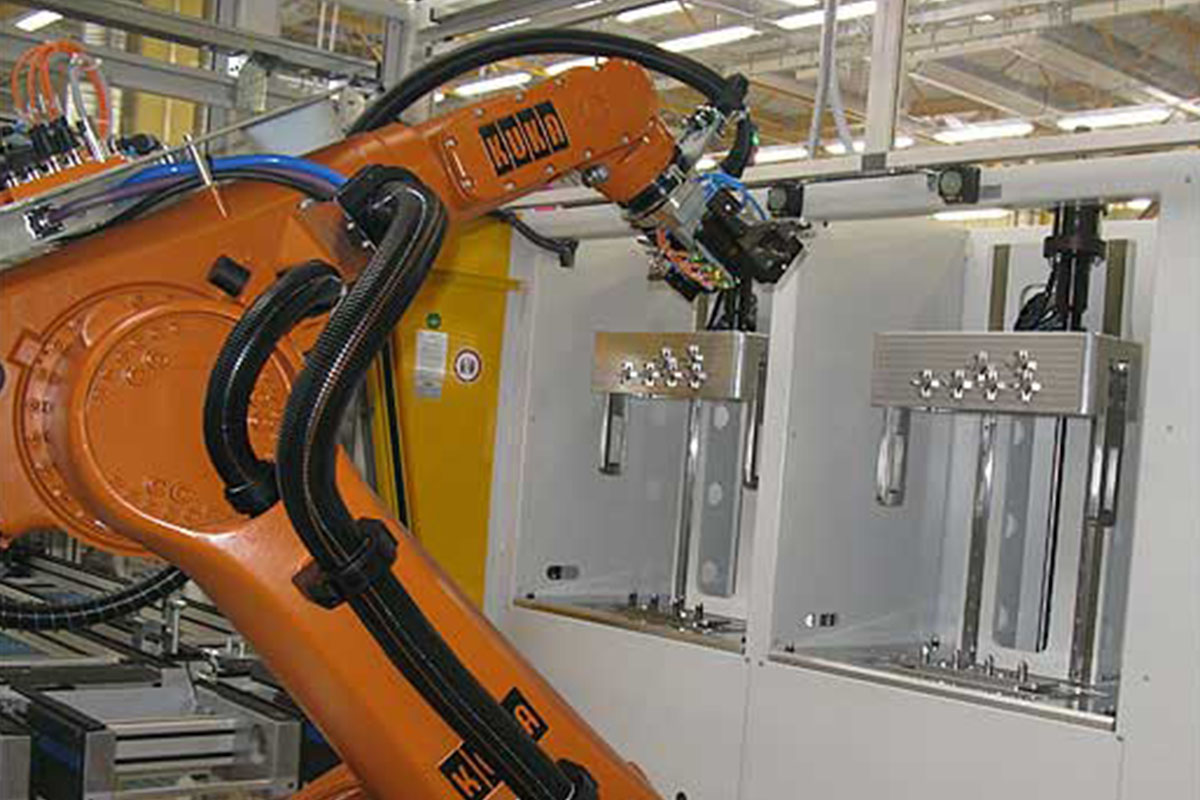
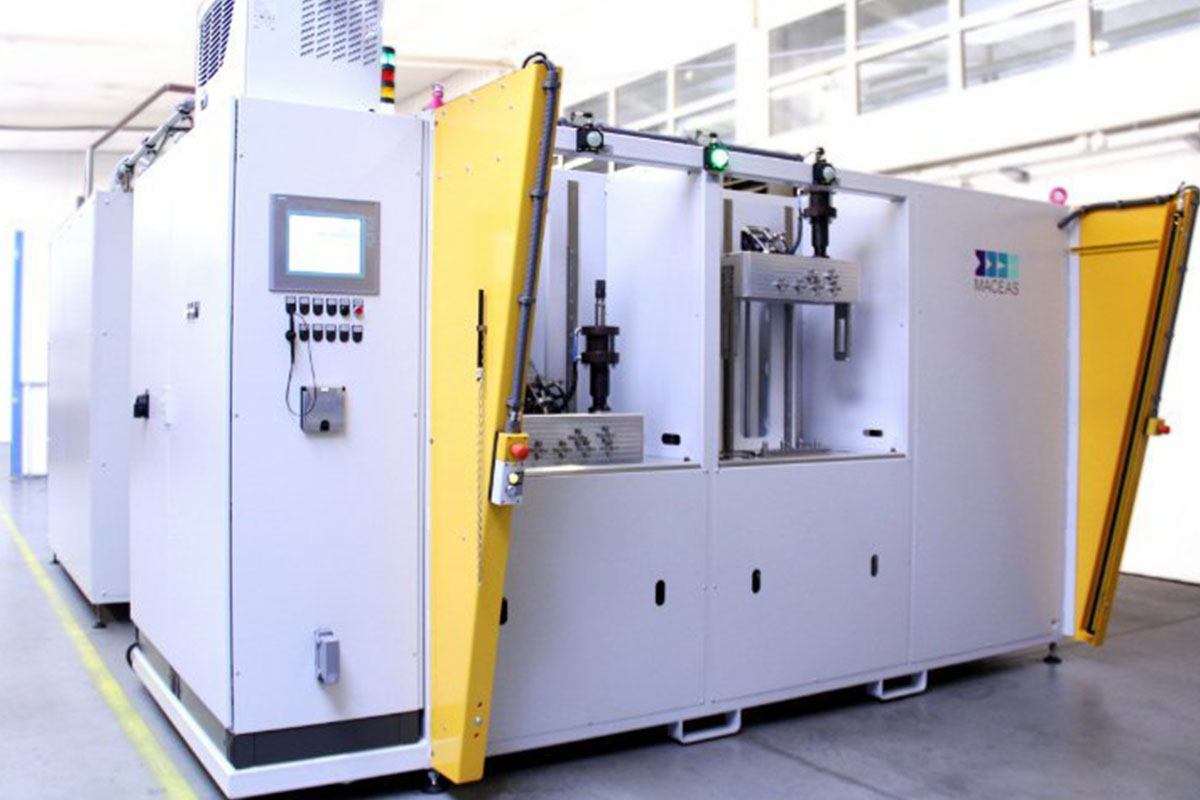
Pipe systems
There are many different pipe systems within a vehicle. These include air conditioning, fuel distribution (e.g., for the distribution of hydrogen) and cooling of the battery modules and fuel cells.
Helium Leak Test for Filler Pipes
Helium Leak Test for Filler Pipes
All pipes within a vehicle are subject to different quality and test requirements. Among other things, this involves testing for high pressures and / or very low leakage rates. Refrigerants contain many toxic substances and therefore the pipes and hoses carrying the refrigerant must also be checked for leaks. We offer modular and scalable helium vacuum test stands that enable the detection of very low leakage rates.
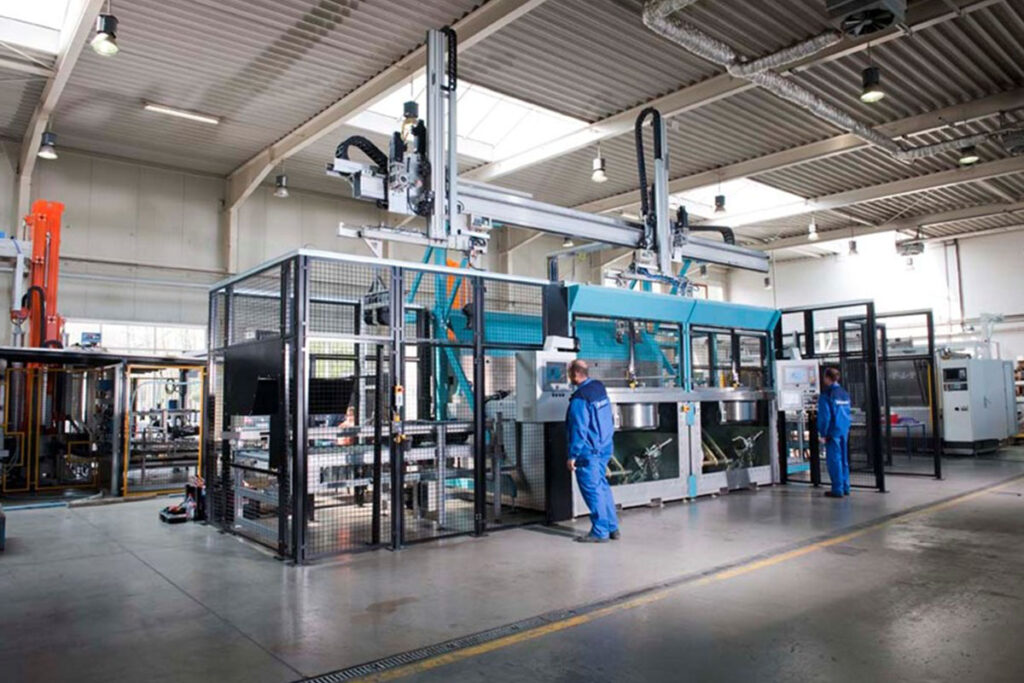
Compressors
Compressors supply the fuel cell with the necessary amount of air for reaction, which enables the fuel cell to achieve optimal operating and performance conditions. The components of a compressor are subject to high requirements, including in terms of tightness. Our leak tests with helium or ultrasound enable the leak test of all components of a compressor or other parts.
Helium leak testing
The leak test with the help of helium enables a process-safe, reliable and very precise leak test even in series production. Two methods are used, the helium leak test in a vacuum or under atmosphere. Theoretically, leak rates of up to 10-12 mbar*l/s can be detected (detection limit of the mass spectrometer). Typical leak testing applications in a vacuum or under atmosphere, however, are in the range of 10-2 – 10-7mbar*l/s. Both leak testing methods can be fully automated.
Ultrasonic leak testing
The ultrasonic leak test is the further development and automation of the so-called “bicycle tube” method or visual leak test by a worker on site. In this way, the formerly subjective worker water bath test is replaced by an objective, semi or fully automatic ultrasonic leak test system. This method not only enables leakage to be detected but also to localize it, and that at leakage rates up to 10-5 mbar*l/s. This test method can be used universally and can also be used in industrial series production in a wide variety of industries.
Assembly lines
For the production and assembly of complex products that place high demands on the process and product quality, complex assembly devices are often required and several different devices must be linked to form a complete production line. A large number of interfaces and the material flow between the devices must be planned and implemented as efficiently as possible. This involves both partially and fully automated solutions, always with the integration of test procedures, test tools and a corresponding leak test. This claim is achieved through the complete solution from a single source that we can offer you.
Lorem ipsum dolor sit amet, consetetur sadipscing elitr, sed diam nonumy eirmod tempor invidunt ut labore et dolore magna aliquyam erat, sed diam voluptua. At vero eos et accusam et justo duo dolores et ea rebum.
Stet clita kasd gubergren, no sea takimata sanctus est Lorem ipsum dolor sit amet. Lorem ipsum dolor sit amet, consetetur sadipscing elitr, sed diam nonumy eirmod tempor invidunt ut labore et dolore magna aliquyam erat, sed diam voluptua. At vero eos et accusam et justo duo dolores et ea rebum. Stet clita kasd gubergren, no sea takimata sanctus est Lorem ipsum dolor sit amet.
Lorem ipsum dolor sit amet, consetetur sadipscing elitr, sed diam nonumy eirmod tempor invidunt ut labore et dolore magna aliquyam erat, sed diam voluptua. At vero eos et accusam et justo duo dolores et ea rebum.
Lorem ipsum dolor sit amet consetetur
- Testing of end (cooler) and dummy plates
- Laser marking
- Transport systems to supply and discharge test parts
- Robot handling for loading and unloading of parts
Contact us for more information
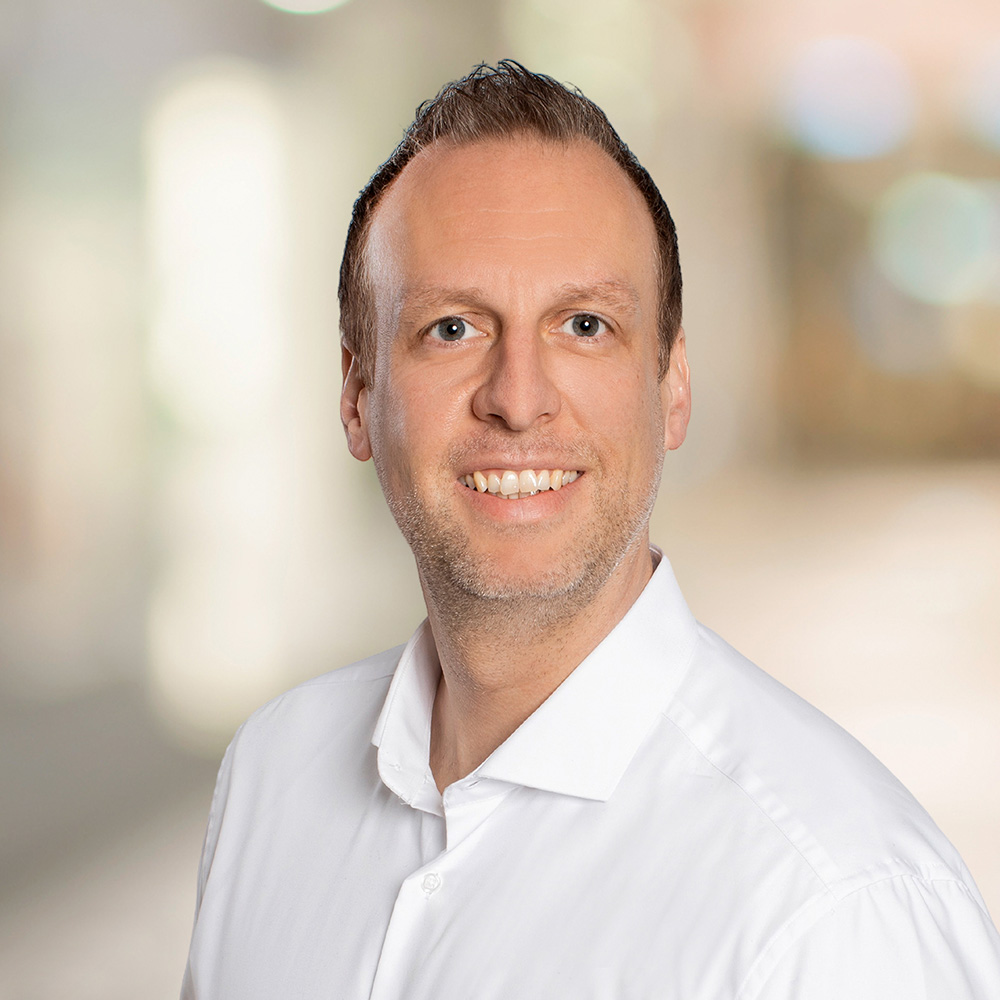
Daniel Schönbohm
Managing Director
MACEAS